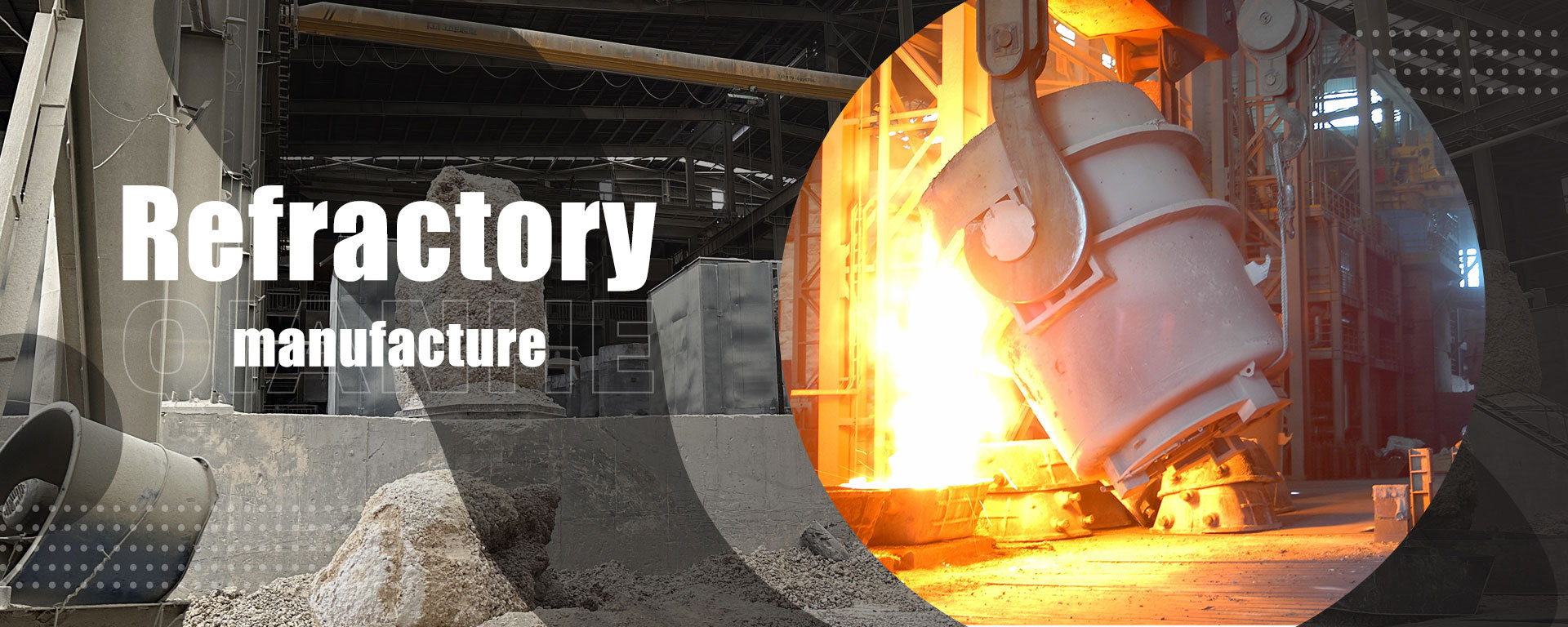
97 98 Fused Magnesite With Large Crystal Grain
1. fused magnesia, as an important refractory material, has excellent characteristics such as high-temperature resistance, corrosion resistance, wear resistance, thermal conductivity, and insulation.
2.Fused Magnesium has a wide range of applications in high-temperature industries, providing a stable and reliable material foundation for many processes.
3With the continuous advancement of technology, the performance and application areas of electric fused magnesia will continue to expand, making greater contributions to the development of high-temperature industries.
- QianHe Refractories
- Haicheng,Liaoning,China
- within 30 days
- 300000 tons per year
- Information
Fused Magnesium 98 Parameters as below
Regular Fused Magnesia | ||||||||
SPEC | LOI%≤ | SiO%≤ | CaO%≤ | Fe2O3%≤ | AL2O3%≤ | MgO%≥ | B.D(g/cm)≥ | SIZE |
(MM) | ||||||||
98 | 0.1 | 0.6 | 0.8 | 0.5 | 0.1 | 98 | 3.5 | 0-150 |
97.5 | 0.12 | 0.8 | 1 | 0.6 | 0.12 | 97.5 | 3.5 | 0-150 |
97 | 0.15 | 1 | 1.2 | 0.7 | 0.15 | 97 | 3.5 | 0-150 |
96 | 0.2 | 1.5 | 1.5 | 0.9 | 0.2 | 96 | 3.45 | 0-150 |
Fused magnesia has the characteristics of high temperature resistance, corrosion resistance, good thermal conductivity, good wear resistance, low thermal expansion coefficient, and good electrical insulation performance. Therefore, it is widely used in the fields of refractory materials, insulation materials, and electrical equipment.
Fused magnesia has outstanding wear resistance. Its high hardness and wear-resistant characteristics allow it to maintain stable performance in high-speed friction and wear environments. Therefore, fused magnesia is widely used in fields such as abrasives, grinding tools, and cutting tools, improving the lifespan and efficiency of tools.
QianHe Refractories located in Haicheng City,LiaoNing Province,
where is famous for its heavy and rich magnesite mine in the world.
We produce Magnesia Products including fused magnesia ,magnesia oxide ,
2:1 low silicon high calcium fused magnesia ,arge crystal of fused magnesia
and DBM90,DBM92,DBM97.
The production process and procedure of fused magnesium 98 involves several steps. Firstly, raw magnesium ore is extracted from mines and undergoes a purification process to remove impurities. The purified magnesium ore is then crushed into small particles.
Next, the crushed magnesium ore is mixed with a flux material, such as calcium fluoride, to improve the melting properties. This mixture is then loaded into an electric arc furnace, which is heated to extremely high temperatures using electricity.
Once the electric arc furnace reaches the desired temperature, the mixture undergoes a fusion process. The heat generated by the electric arc melts the magnesium ore and flux, resulting in a molten magnesium mixture.
After the fusion process, the molten magnesium mixture is carefully poured into molds or cooled in water to form solid magnesium ingots or granules, depending on the desired product. These ingots or granules are then further processed, such as through milling or grinding, to achieve the desired particle size and shape.
The production of fused magnesium 98 involves the extraction and purification of raw magnesium ore, mixing with flux, melting in an electric arc furnace, shaping into ingots or granules, and quality control testing.