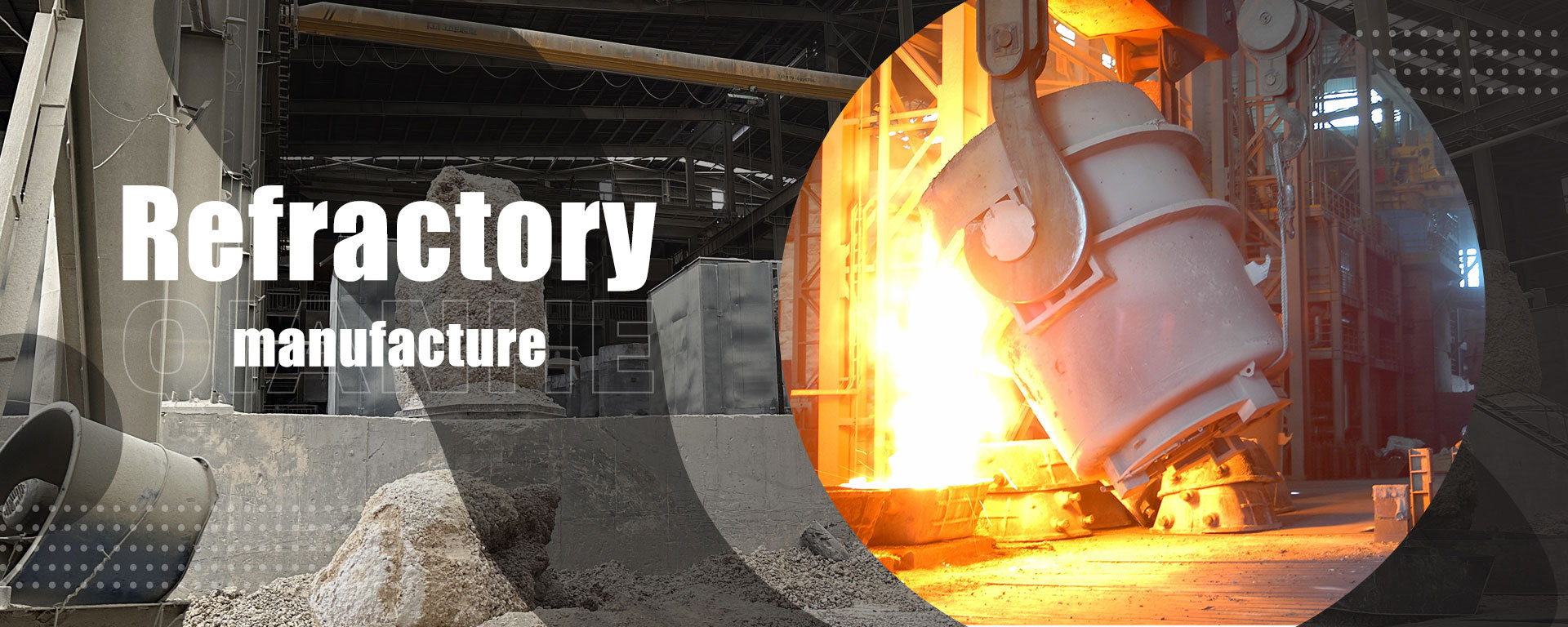
Fused Magnesium For Refractory Bricks
1.97 fused magnesia is widely used in the production of magnesia carbon bricks
2.Strong resistance to corrosion: Fused Magnesium exhibits strong resistance to corrosion from molten metals and slags, making it an ideal material for lining furnaces and crucibles.
3.Good electrical insulation: Electric fused magnesia sand has good electrical insulation properties, making it suitable for use in electrical insulation applications.
- QianHe Refractories
- Haicheng,Liaoning,China
- within 30 days
- 300000 tons per year
- Information
Regular Fused Magnesia | ||||||||
SPEC | LOI%≤ | SiO%≤ | CaO%≤ | Fe2O3%≤ | AL2O3%≤ | MgO%≥ | B.D(g/cm)≥ | SIZE |
(MM) | ||||||||
98 | 0.1 | 0.6 | 0.8 | 0.5 | 0.1 | 98 | 3.5 | 0-150 |
97.5 | 0.12 | 0.8 | 1 | 0.6 | 0.12 | 97.5 | 3.5 | 0-150 |
97 | 0.15 | 1 | 1.2 | 0.7 | 0.15 | 97 | 3.5 | 0-150 |
96 | 0.2 | 1.5 | 1.5 | 0.9 | 0.2 | 96 | 3.45 | 0-150 |
1.Characteristics of fused magnesium
Electric fusion magnesium has excellent properties that make it highly desirable in industries such as aerospace, automotive, electronics, and construction. It has a low density, high strength-to-weight ratio, and good corrosion resistance, making it an ideal material for lightweight structural components. Additionally, it has good thermal and electrical conductivity, making it suitable for applications in heat sinks, electrical connectors, and other electronic components.
2.Characteristics of fused magnesium
electric fusion magnesium can be easily machined, welded, and formed, allowing for versatile applications in different industries. Its unique combination of properties makes it a preferred choice in the manufacturing of aircraft components, automobile parts, consumer electronics, and various other products.
QianHe Refractories located in Haicheng City,LiaoNing Province,
where is famous for its heavy and rich magnesite mine in the world.
We produce Magnesia Products including fused magnesia ,magnesia oxide ,
2:1 low silicon high calcium fused magnesia ,arge crystal of fused magnesia
and DBM90,DBM92,DBM97.
The production process of fire-resistant material electric fused magnesia products typically involves the following steps:
1. Raw material preparation: The first step is to obtain high-quality magnesite ore. The ore is then crushed, ground, and screened to ensure consistent particle size and purity.
2. Calcination: The crushed magnesite is then heated in a rotary kiln or a shaft kiln at high temperatures (around 1500°C) to remove impurities and convert it into magnesia clinker.
3. Briquetting: The magnesia clinker is mixed with a binder and pressed into briquettes or pellets of the desired shape and size. This process improves the density and strength of the final product.
4. Electric melting: The briquettes or pellets are then placed in an electric arc furnace. The furnace is heated to extremely high temperatures (above 2800°C) using electric current. This intense heat causes the magnesia to melt and form a liquid.
5. Cooling and solidification: Once the magnesia has melted, it is allowed to cool and solidify. This process may involve controlled cooling rates to achieve desired crystal structures and minimize defects.
6. Crushing and grading: The solidified magnesia is crushed into smaller particles and then graded according to particle size. This ensures uniformity and consistency in the final product.
Packaging and storage: The final product is packaged in suitable containers or bags for storage and transportation. Proper labeling and documentation are also important for quality control and traceability.
Throughout the production process, quality control measures are implemented to ensure that the final product meets the required specifications and performance standards. These may include chemical analysis, physical property testing, and visual inspection.